Tales from the Leather Bench: Kukri sheath restoration
- Alicia Adams
- Jun 27, 2024
- 5 min read
Updated: Jul 3, 2024
While Chris spends his days bending blades to his will over the anvil, my own craft takes place in my little home workshop, where I make scabbards, sword belts, baldrics and protective gear to send to fencers around the world.
While much of my work is sold as seen, I really enjoy taking the occasional commission. I find that these projects always have a story behind them: some tooling with a particular meaning behind it, or a new scabbard for a long-loved sword.
A sentimental treasure
This particular project was no exception, and it gave me a chance to apply my leatherworking skills to restoration for the first time. I was contacted by a member of my fencing club, who was looking after a Nepali kukri belonging to his grandparents.
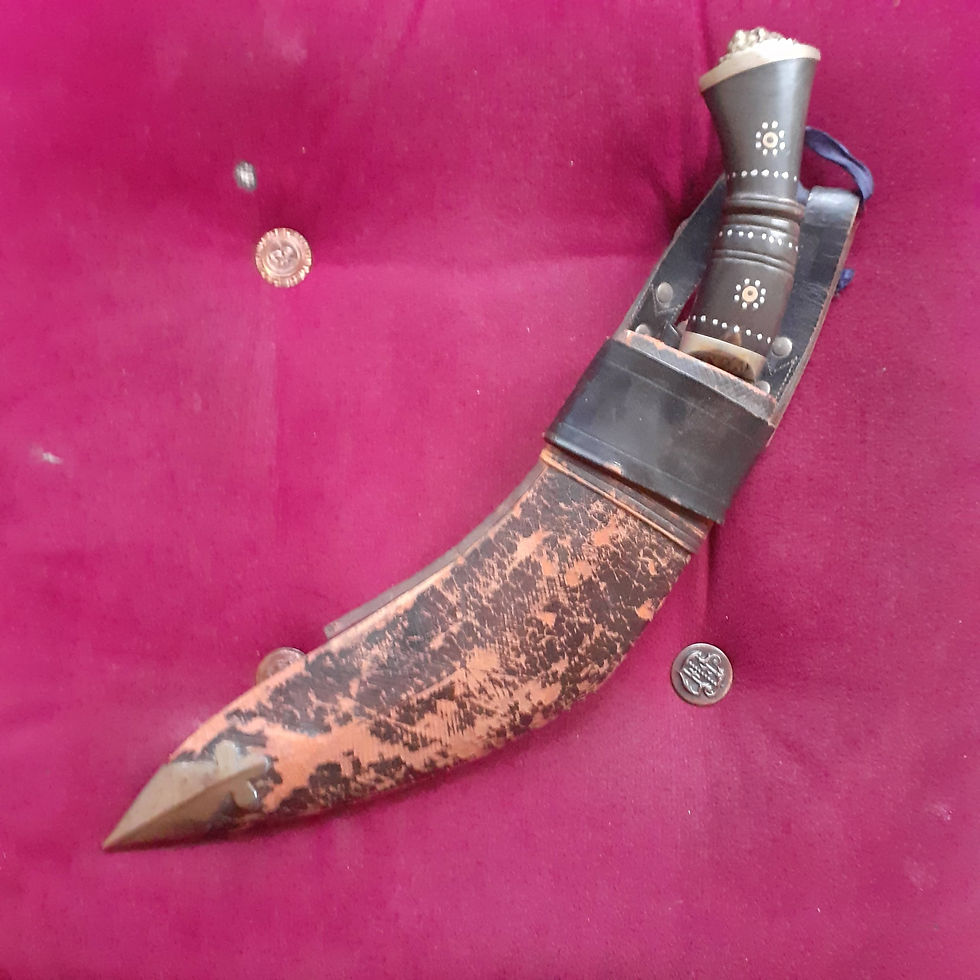
He explained that the kukri had been given to his grandparents as a wedding gift by friends who have since passed away. Over time the knife itself had stayed bright and sharp, but the leather and wood sheath had fallen into disrepair. He asked me if I could restore the sheath to something of its former glory, as a gift for his grandparents' wedding anniversary.
Working on something with not only years behind it but also a great deal of sentimental value was a new challenge to me, calling for utmost care and patience. However, in taking my time over the project, I learned new skills and an appreciation for the craftsmanship behind vintage "tourist" weaponry.
Out With the Old
Once I had removed the belt frog, my first challenge with the kukri sheath project was the point of no return: stripping the old leather outer from the wooden core, and seeing what was salvageable. I carefully documented each part of the process, taking photos of everything from the tooled patterning to the stitched spine so that I could reproduce it in kind.
The work began to feel like an exercise in archaeology, carefully peeling and flaking away dry kidskin, and discovering new structural elements underneath. It was certainly somewhat bittersweet to remove the damaged decoration, knowing it had been carefully cut and pressed by a fellow craftsman decades ago, but I vowed to reproduce the pattern as best I could on the new skin.
To my delight, the wooden core was in great condition under the dry leather, and could be reused. I was happy to rescue not only the brass chape from the tip of the sheath, but a metal reinforcement strip that followed the inner curve of the core, acting as a barrier to stop the knife from breaking through the core if drawn at the wrong angle.
It has pockets!
By far the most interesting aspect of the sheath was its pair of byknife pockets, each housing a small, intricately decorated knife to match the kukri. While there are some fantastic examples of European scabbards featuring byknife pockets, I have not until now had the chance to reproduce one.
Having the chance to take apart an existing byknife pocket was the best possible tutelage I could have in this craft, and I discovered various tricks of the trade as I excavated. From stitches passing through the wood of the core to small metal tacks to a thin piece of thong stopping the pockets from shifting under the sheath's kidskin outer, I took notes on each method, ready to recreate them.
A Second Skin
While the original leather elements, including the byknife pockets, were too dry and damaged to be reused, they did make for fantastic templates by which I could cut new pieces.
I chose 2mm leather strapping for the mouths of the byknife pockets, with tubes made from a 1mm kidskin, reinforced at the base. This combination kept the pockets flexible, allowing them to lie flat when empty, but ensured that the smaller blades would not punch through if put away hastily.
Once I had reattached the pockets, using the original stitch holes in the core, and reattached the brass strip to the wood, I set about covering the whole in a tightly fitted layer of kidskin. The extreme curve of the core and the addition of the byknife pouches made this a more challenging job than I am accustomed to with sword scabbards, but a lot of soaking, stretching and patience eventually resulted in a smooth finish.
Finishing touches
Once I was happy with the fit of the leather outer, it was time to stitch the seam. I cut the seam flat to the wooden core, and finished it with a butted corpse stitch. A good once-over with a burnisher flattened down the edges and gave a smooth finish.
Next, I needed to decorate the sheath. Referring to my photos and sketches from the original outer, I recreated the simple yet painstaking hand-tooled lines on the front face. These came together in what felt like a snakeskin pattern over the length of the sheath, brought out by burnishing. I then cut a thin leather strap to tie around the sheath and byknife pockets, attaching it in the same place where the original had been, and securing it with a stitch.
The original brass chape fit beautifully over the new leather outer, and with a bit of a polish gleamed proudly against the dark brown sheath, matching the brass pins in the handle of the kukri itself.
Last but not least, I used the original frog pieces as a template to make a new one. The loop of the frog was made from doubled-up 1mm kidskin, while the belt loops were made from 2mm strapping. I used copper rivets to secure the pieces together, and carefully manoeuvred the band over the sheath and byknives.
A Gift Revived
While I was very proud of the sheath's new look and likeness to the original leatherwork, the real proof of the pudding was in how its owners responded. Their grandson was kind enough to send me a video of them opening their "new" gift, and they were delighted to see their treasure revived, calling the leatherwork "a beautiful job".

I passed on a few tips for feeding and polishing the leather, so that this incarnation of the sheath can last a little longer than its predecessor! It's always a shame to see a piece of vintage leatherwork dry out beyond repair, but it was a real honour to give an old crafted item new life, and to learn a few things about knife sheath construction along the way!
If you have a sheath, scabbard or swordbelt that you'd like to have restored or replaced, get in touch with us and I'll happily discuss your requirements!
Please note, this was a special commission, and we do not usually take commissions involving sharps.